Fumigation of biological safety cabinets
2021-06-22 10:03:19
Biosafety cabinets are very familiar to the vast number of research and experimental personnel, but their use and maintenance, especially under the specific conditions of complete fumigation and disinfection is not necessarily well understood, due to many reasons, most laboratories After the biosafety cabinet has been put into use, even for many years, it has not undergone necessary maintenance, and some have even been used in an abnormal state. This leaves a hidden danger to the laboratory biosafety, especially in some specific situations, such as the need to replace the exhaust high-efficiency filter after 3 to 5 years of use, the biosafety cabinet is seriously polluted before the safety cabinet fails and needs to be opened for maintenance. Thorough fumigation is required.
Commonly used disinfectants for fumigation include formaldehyde, hydrogen peroxide, chlorine dioxide, etc. Although formaldehyde is the least expensive, its carcinogenic effects have been increasingly restricted by use, and most people who have used formaldehyde fumigation have headaches. Because the entire safety cabinet is sealed with plastic cloth, the amount of disinfectant required, the placement of biological indicators, neutralizing disinfectant, waiting for a long time, etc., the most worrying is the leakage of formaldehyde and the bio-challenge experiment. Security issues such as success or failure.
There is now a new way to completely replace the traditional formaldehyde fumigation, which uses hydrogen peroxide vapor to sterilize the biosafety cabinet. Usually the generator is connected to the main cabin through a jetting interface. Some models of safety cabinets already provide this interface. At the same time, the door sealing plate seals the front operation port. If neither of these configurations are available, a temporary door seal can be used and the appropriate connection interface is pre-installed, mounted on the front operating port, and hydrogen peroxide vapor is injected through the interface on the door seal. Inside the biosafety cabinet.
Usually the steam circuit is connected to the rear of the safety cabinet exhaust filter, of course the exact type and location of the connection depends on the type of biosafety cabinet with disinfection. When replacing the filter or performing maintenance on the safety cabinet, this connection pushes the hydrogen peroxide vapor through the exhaust filter of the safety cabinet and thoroughly sterilizes it.
It is also feasible to disinfect only the main compartment and can be used to kill all microorganisms in the cabin and under the workbench before the next experiment to avoid cross-contamination. This solution has a shorter sterilization cycle time than the main filter and uses less hydrogen peroxide.
All biosafety cabinets have more or less gas leaks. To ensure process safety, the hydrogen peroxide generator can maintain a small negative pressure condition, ensuring that hydrogen peroxide vapor does not get from the tank during the sterilization process. The body leaked into the laboratory. This function is obtained by attaching a small pressure control tube to the door seal plate before disinfection.
The figure below shows a typical biosafety cabinet disinfection configuration method.
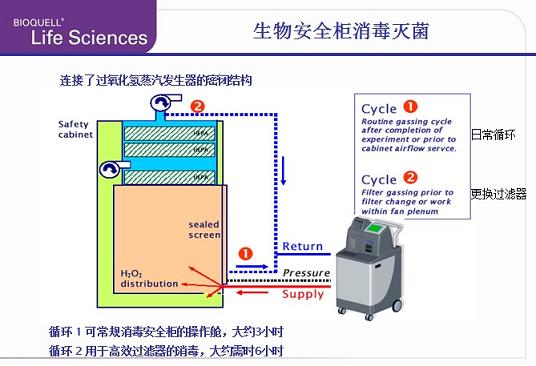
For the three-stage biosafety cabinet, the steam can be injected into the cabin through the installed transmission hatch through the small air supply high-efficiency filter, and the steam returned by the exhaust pipe forms a closed loop, and the gas supply and exhaust filter are And disinfection.
Bioquell even offers a more complete solution, the Mircoflow series of high-grade biosafety or microbiological laboratory secondary biosafety cabinets, designed and manufactured according to BS5726 / EN12469 standards, and operated by independent validation of the Applied Microbiology Research Center CAMR The highest level of protection for the sample and the sample, the Bioquell Clarus series of hydrogen peroxide vapor generators are integrated in the hardware and software system, including the introduction of gas into the operating compartment and downstream from the exhaust high efficiency filter, fully sterilizing the working chamber and exhaust HEPA filter.
Introduction to HPV Technology
Hydrogen peroxide vapor (HPV) disinfection technology is rapidly becoming the biological purification method of the pharmaceutical, biotechnology and healthcare industries, achieving a 6-log kill rate for the same biological indicator as the pressure cooker, Bacillus stearothermophilus. Biological purification of the facility can be carried out with extensive disinfection products and services during commissioning or downtime.
Bioquell uses the patented Clarus dual-cycle technology combined with PLC program control to optimize the effectiveness of the sterilization cycle. When hydrogen peroxide forms micro-condensation on the surface of the room or cabin, biological disinfection is achieved. At this stage, a naked eye can be seen under the microscope. Invisible submicron-scale thin layers of hydrogen peroxide, scientific studies have confirmed that this low-temperature, residue-free process has begun to kill microorganisms in the steam generation phase. The formation of micro-condensation ensures that the optimal conditions for microbial killing are formed, and when the condensation point is reached, the time (D value) for reducing one log-level (1-log) microorganism is the shortest. From the sterilization kinetic curve, it can be seen that the number of microorganisms drops sharply, and with the formation of microcondensation, the biological indicator number curve becomes drastically reduced from soothing.
In some industries, a biologically clean environment is very important, and Bioquell's HPV technology has significant advantages over other sterilization methods. Traditional disinfection methods and disinfectants such as formaldehyde fumigation are not only lengthy but also very dangerous. Formaldehyde has been classified by the World Health Organization as a carcinogen for humans. Formaldehyde disinfection is usually recommended for 12 hours of contact time in a room, followed by a long row. Gas and ventilation process (about 24 hours). In contrast, the disinfection cycle of hydrogen peroxide in the room can be as low as 2 hours, and the entire facility of about 8000 m 3 can be completed in as little as 24 hours.
Bioquell's hydrogen peroxide vapor (HPV) disinfection process is fast, residue-free and safe, producing only water and oxygen. HPV also has a wide range of material suitability compared to other disinfectants, meaning less risk of damage to buildings and can be used as fixtures and equipment for the facility.
In the life sciences and food industries, the HPV disinfection process is a very good disinfection method and is accepted by major regulatory agencies. A complete material compatibility guide is available upon request. For a wide range of microorganisms affecting life sciences, food and other industries, HPV disinfection technology has been proven to have broad-spectrum sterilization and, if required, a complete guide to disinfection.
Bioquell's disinfection equipment and services offer a variety of solutions for users to choose from. In fact, the Bioquell hydrogen peroxide steam generator is like a high-end SLR camera that can be operated automatically or manually. Develop more different applications on your own and create more value for your investment.
You can use Lishida Sushi Vinegar for different dishes.First,you could use for rice to make it yummy.Sushi Vinegar is a great seasoning sauce for recipes,such as salad dressing,chicken marinating and stir frying pork.
Sushi Rice Seasoning,Sushi Rice Vinegar,Sushi Seasoning,Sushi Seasoning For Rice
KAIPING CITY LISHIDA FLAVOURING&FOOD CO.,LTD , https://www.lishidafood.com